Asphalt Paving Charleston SC can significantly impact how long it will last. The mix, thickness, and compaction of the asphalt all affect how long it will hold up to traffic and weather elements.
Look for a paving contractor offering these services to ensure you get a good quality job.
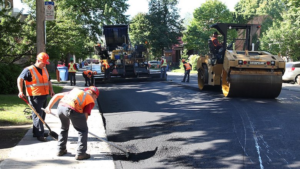
Asphalt is a popular choice for paving because of its durability. It is a highly versatile material that can be used for roads, driveways, and parking lots. Compared to concrete, which cracks easily due to cold weather and water damage, asphalt lasts much longer. A well-maintained asphalt surface can last up to 40 years or more.
One of the reasons for asphalt’s durability is its strength and ability to withstand heavy vehicle traffic. It can withstand repeated cycles of loading and unloading without suffering significant damage. However, it’s important to keep in mind that the durability of asphalt is influenced by environmental factors, such as temperature, rainfall, and sun exposure.
When mixed with the right amount of aggregate, asphalt can withstand high temperatures. However, if the pavement is exposed to extreme temperatures for long periods of time, it can weaken its structure and lead to premature failure. Heat can also cause asphalt to oxidize, which reduces its stiffness and resistance to deformation. This can also cause the pavement to become rutted and damaged.
In order to prevent this, contractors can use an additive that increases the stiffness of the asphalt mixture. Various materials have been used for this purpose, including recycled rubber, crushed glass, and treated swine manure. This additive is expensive, but it can greatly improve the durability of asphalt pavements.
Another way to increase the durability of asphalt is by increasing its in-place density. While higher densities are typically only achieved in high-quality, newer construction methods, they can help to extend the life of asphalt pavements by preventing bottom-up fatigue distress.
The process of laying down asphalt starts with grading the site. Contractors slope the pavement toward grassy areas to help drainage and prevent water buildup underneath the pavement. The next step is to put down a base layer, which is made of dense, load-bearing aggregates. A binder layer is then placed on top of this. Typically, this is made of finer, more compacted asphalt.
In addition to ensuring that the asphalt meets specifications and quality standards, testing is done throughout the mixing process to check for proper consistency. This allows the contractor to make adjustments as needed and ensure that the pavement will be able to meet its intended function.
Asphalt might seem dull at first glance, but it has a dark beauty that stands out against concrete buildings and landscaping. It’s sleek surface is also easy to clean and resists stains and damage better than some other paving materials. With its ability to be easily modified, asphalt offers design flexibility and a range of creative solutions that can make your commercial property more visually appealing.
The basic composition of asphalt includes stone (aggregate), sand, additives and liquid asphalt or bitumen to hold the aggregates together. These ingredients are mixed in batches at special processing plants. Plant operators measure and blend the ingredients based on the specific climate at the project site. Hot mix asphalt is typically used for high-traffic areas and provides superior durability. Cold mix asphalt is less expensive and suitable for smaller projects.
Another unique attribute of asphalt is its noise-reducing properties. The material is quieter than other paving options, such as concrete, because it absorbs sound instead of reflecting it. Its acoustic qualities are a major contributor to why it is often used on roads and highways.
With its innate beauty and range of design options, asphalt is the perfect choice for any outdoor space. Whether it’s a parking lot, road or other walkway, it can add style and sophistication to any business. Its versatility also makes it an attractive option for public spaces, allowing for easy-to-read signage and eye-catching colors that will attract customers to your business.
Asphalt can be customized to meet your specific aesthetic needs by using a variety of sealing, crack filling, resurfacing and line painting techniques. By adding these features to your pavement, you can customize its appearance and extend its longevity. For example, you can seal asphalt to protect it from water, oil, and sunlight. Asphalt surface treating also helps reduce its permeability and improves traction.
Asphalt is a budget-friendly material that provides great value to your property. The comparatively low cost of asphalt makes it an ideal option for residential driveways, sidewalks, parking lots and roads. It also looks beautiful and lasts longer than other paving materials such as concrete. Asphalt paving requires regular maintenance to keep it looking good and functioning properly. Regular sealing and repairs to cracks and holes will ensure your pavement retains its beauty for a long time.
The material is easy to work with and does not require as much labor as concrete. It is also more affordable to maintain because it is less prone to cracking. Asphalt pavement can be easily repaired using a special crack filler that is available at your local hardware or home improvement store.
This product works by bonding the cracks with an adhesive substance, which will help prevent water from seeping through to the sub base. This will prolong the life of your asphalt surface and prevent costly repairs in the future.
Another benefit of asphalt is that it dries quicker than concrete. This means you can get back on your road faster and avoid the orange barrels and lane closures that are usually associated with other types of paving projects. It is also a more environmentally friendly material since it uses recycled materials and produces less fumes during paving.
Asphalt is made up of stone (aggregate) sand, additives and liquid asphalt (petroleum). Liquid asphalt is what holds the aggregate together. The mix is heated at an asphalt plant to make it hot and then transported by dump trucks to the paving site. It is kept hot during the entire paving process to prevent it from cooling, which would cause it to lose its binding properties.
Cold asphalt mixes are used for patching and lesser-trafficked service roads. These are produced by emulsifying hard grade blown bitumen in water with an emulsifying agent. This mixture stays soft in cold temperatures and repels water, which is why it is primarily used for pothole repair. This type of asphalt is not as durable as HMA and has a shorter lifespan, but it offers similar benefits to homeowners.
The asphalt paving process requires the use of power machinery and heavy equipment, so safety is always a priority. Workers must wear proper personal protective equipment to avoid exposure to physical, environmental and chemical hazards.
Typical PPE includes thermally-insulated gloves, coveralls and boots, to protect the skin from contact with hot materials. It’s also important to keep a fire extinguisher nearby, preferably rated type B or ABC. It should be easily accessible to employees.
Asphalt contains petroleum, so it is flammable. It’s important to avoid smoking and using open flames near the asphalt. Make sure to have a firebreak in place if the area gets too close to a flame source. Workers should also be careful around electrical lines, which could cause an electrocution if they are touched.
Working with asphalt is hazardous because it’s extremely greasy and sticky. If it comes into contact with bare skin, it can burn the skin and irritate the eyes and respiratory tract. It can also soak into clothing, which can leave behind toxic stains and odors.
Paving should be done in dry conditions with moderate temperatures. Extreme temperatures can make the asphalt too soft to work with, while extreme cold can prevent it from curing properly. Workers should look out for potential tripping hazards, like manholes and catch basins, and mark them clearly. It’s also important to check the weather report before starting a project, as rain can affect the quality of the finished product.
The first step in the paving process is to grade the road. Contractors slope the surface to allow water to drain away from the road and prevent it from sitting on the asphalt. A sub-base layer is then laid, which consists of crushed stones that are typically mixed with bitumen. This helps reduce rutting by evenly distributing traffic and environmental loads.
The binder course is then put down, which provides stability by combining qualities of durability and stiffness. It should be designed to withstand the highest shear stresses to minimize rutting, while still allowing sufficient stone-on-stone contact and a flexible base layer.